用 工匠精神(shén)
做 好 每 個 零 件
一、有機玻璃零件加工難題(tí)
有機玻璃別名為聚乙酸乙烯酯,具備不錯的透光度(dù)和(hé)有機(jī)化學可靠性,耐腐蝕,且規格平穩、便於成型,因此在航天航空(kōng)、化工廠和診(zhěn)療(liáo)等行業都是有廣泛運用。在具體生產製造運用中,有機玻璃產品(pǐn)零件大多數能夠立即(jí)鑄造成形,但有一些樣子獨特、規格精密度和外表粗糙度規定較高的零件,通常必須開展機械設備加工(gōng)。但有機玻璃原材料與金屬複(fù)合材料的物(wù)理性能有很大差別(bié),其材質較脆,具備空(kōng)缺敏感度,在地(dì)應力功效下易裂開。
圖1所顯示零(líng)件燒杯是典型性的有機玻璃零(líng)件,且為空心厚壁(bì)構造。其規格精密度規定較高,技術標準加(jiā)工後維持材料原來透(tòu)光性,達到精確測量測量範圍(wéi)的要求。該零件選用加(jiā)工中心開展加工時雖便於成型(xíng),但加工工(gōng)藝主要參數和工藝流程挑選不那時候,非常容易發生裂痕等缺點(diǎn),導致零件損毀。此外,其(qí)表層處(chù)理(lǐ)方式的挑選尤其重要,實際操(cāo)作不那時候,表層呈撕破狀,非常容易“擦毛”,喪(sàng)失有機玻璃原來(lái)的透光性,不(bú)能滿足技術標準。
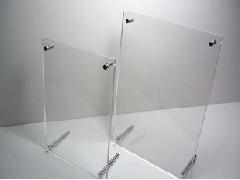
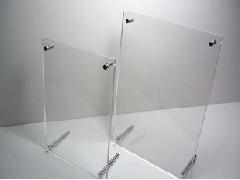
二、零件加工的危害各種因素
(1)鑽削熱對有機玻璃加工(gōng)的(de)危害很大,具體表現在(zài)下列兩層麵:①因為有機玻璃的傳熱性很差,傳熱係數僅(jǐn)為(wéi)一般金屬複合材料的1/450~1/175,因此鑽削(xuē)加工(gōng)中造成的鑽削熱沒法迅速地釋放,發(fā)熱量累積在數控刀片與產品工件的觸碰位置,造成數控刀片損壞加重。與此(cǐ)同(tóng)時有機玻璃的線(xiàn)膨脹係數比一般金屬材料要大1.5~2倍(bèi),熱膨脹係數(shù)大概為100℃上下,過高的鑽削熱使有機玻璃容積產(chǎn)生變化和玻璃化,使加工精(jīng)密度降低,沒(méi)法做到加工規定。與此同時有機玻璃的容積澎(péng)漲又加重了數(shù)控刀片(piàn)與產品工件的磨擦,造成鑽(zuàn)削熱進一步上升,產生惡循環。②因為有機玻璃的溶點較低,僅有160~200℃,歸屬於熱固(gù)性原材料(liào)。鑽削加(jiā)工中過高的鑽削熱非常容(róng)易使加工(gōng)表(biǎo)層(céng)造(zào)成熔(róng)結狀況。主要表現(xiàn)為零件加工內螺紋時,排熱標準較弱,表(biǎo)層非常容易“擦毛(máo)”,展(zhǎn)現出細微的撕破紋,誤認為加工時原材料質脆造成的細微裂痕或原材料自身(shēn)的(de)內部(bù)缺點,但透光性或滲漏查驗時,均無泄漏,零件的清晰度沒法做(zuò)到技術標準,加工(gōng)成型後產品工件表層發(fā)汙,遠沒有零件材料自身的層次感。
(2)加工主要參數對有機玻璃加工的危(wēi)害。有機玻璃常溫狀態歸屬於硬而脆的原材料,而該(gāi)零件具備厚壁構造,鑽削加工全過程中,因鑽(zuàn)削主(zhǔ)要參數挑選不合理(lǐ)造成切削速度不穩定,進(jìn)而造成零件造成裂痕,乃至碎裂。
(3)有機玻(bō)璃鑽削加工後外表粗糙度較弱。由於有機(jī)玻璃的強度較小,鑽削加工後的外表粗糙度較弱。鑽削加工後的零件為(wéi)了更好地確保技術標準,需選用獨特研磨材料及加工工藝才可以完成(chéng)。
三、原加工加工工藝的不夠
按該工序開展加工時,內孔的規(guī)格精密度及外表粗糙度易確保,能夠挑選較高的切(qiē)削(xuē)用量,為1800~2000r/min,且切削速度為0.08~0.30mm/r。可是有兩個存在的不足:①加工內(nèi)螺紋時,發覺不論怎樣調節打孔(kǒng)時(shí)的(de)切削速度,且確保充裕的製冷(lěng)時,內孔表層均不一樣水平地展現出毛(máo)刺,試著打磨拋光後,表層發汙,不能滿足技術標準(zhǔn)中的清(qīng)晰度。經剖析,該零件內螺紋(wén)深達135毫米,加工內螺紋時,受鑽削標(biāo)準(zhǔn)的(de)限定,鑽削熱沒法迅速釋放,即便確保(bǎo)充裕的切削油,或是沒法產生合理的流動性循環係統,導(dǎo)致鑽削(xuē)熱累積,再加上原材料自(zì)身的特點,其材質較脆,屬熱固性塑料,受熱後即變軟,受冷後又凝結硬實,最後(hòu)鑽削溫控不合理造成部分地區變軟形變和脆裂,導致表麵不光滑(huá),沒法再度解(jiě)決。②內孔成型後加工內螺紋的另(lìng)一個缺(quē)點,是因鑽削深層過(guò)大,切削速度過大。而(ér)這時的零件內孔已加工結束,加工內螺紋產生厚壁構造時,沒法承擔過大的(de)切削速度而非(fēi)常容易造成發(fā)生裂痕或碎裂。
四、改善後的加工加工工藝
為了更(gèng)好地確保零件的規格精密度、外表(biǎo)粗糙度及技術標(biāo)準,提(tí)升(shēng)零件的加工(gōng)達標率,試(shì)著著在加工零件內(nèi)孔和內孔槽口槽後,先加工內螺紋,為防止原材料自身的延展性回彈力,操縱銑削切削速度(dù)為0.05~0.08mm,與此同時嚴控切削油澆築(zhù)的速度和追隨性,保(bǎo)證(zhèng)打孔(kǒng)加工時鑽(zuàn)削溫度的一致性。內(nèi)螺紋(wén)加工結束後,應(yīng)用槽(cáo)口精準定位輔助工作服,如圖2所顯示,運用頂級抵住槽(cáo)口精準定(dìng)位(wèi)工作(zuò)服的輔助管理中心孔,確(què)保內孔加工時的徑向限位開關。先加工軸直徑φ50毫米後,運用切割刀加工偏刀的避讓室內空間(jiān),隨後(hòu)立即一次(cì)加工成型φ20毫米直徑規格,進行零件的鑽削加工(gōng)。
變動加工工藝流程後,發覺零件表(biǎo)層(céng)不會(huì)有微(wēi)小脆(cuì)裂痕,且無因鑽削溫控不合理導致變軟形變、原材料擦抹錯(cuò)亂狀況,但表層發汙,無透光性(xìng)感,沒有有機玻璃原來的清晰度,不能滿足零件的技術標準,還必(bì)須進一步(bù)開展打磨拋(pāo)光解決。
五、零件(jiàn)打磨拋光加工工藝
先將零件(jiàn)運用水磨砂紙(zhǐ)打磨拋光,將(jiāng)零件表層(céng)的加工刀(dāo)紋和刮痕磨去,但表層呈做霧化(huà)狀,沒法完成清晰度的技術標準。曆經幾類拋(pāo)光(guāng)材料比照後,最後選用軟亞麻布(bù)混塗美白牙膏的打磨拋光方法(fǎ),因零(líng)件內螺紋直徑(jìng)小,將家裏(lǐ)應用的(de)竹筷從正(zhèng)中間割開(kāi),盤繞軟亞麻布,將美白牙膏和水按一定占比(bǐ)混和均勻後做為粗(cū)蠟,調整適度的時速(sù),沿軸向(xiàng)勻稱拓(tuò)寬至內螺(luó)紋內孔,加工後表層無銑(xǐ)削加工印痕,晶瑩透亮,完成了零件的清(qīng)晰度要求(qiú)。